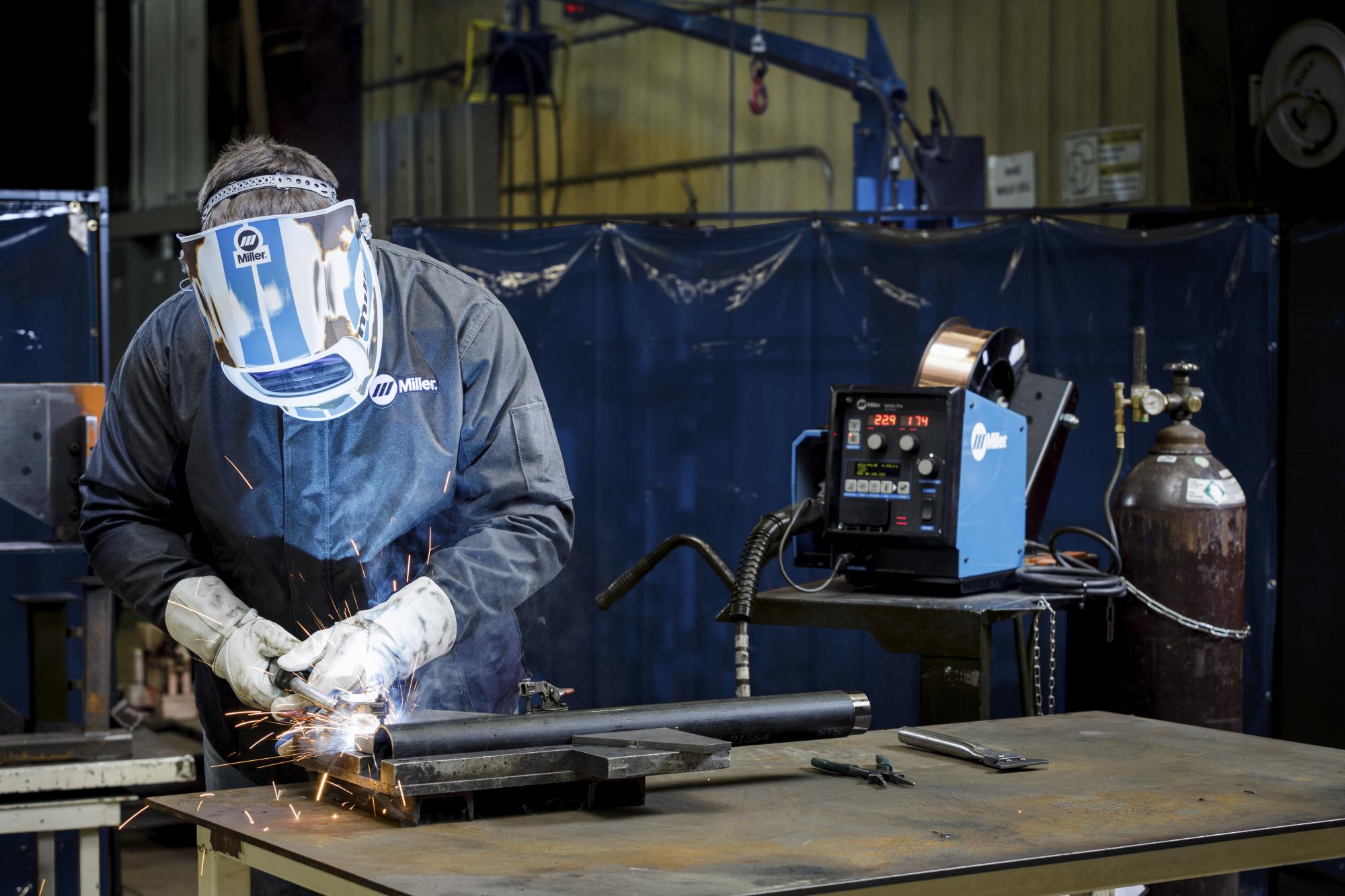
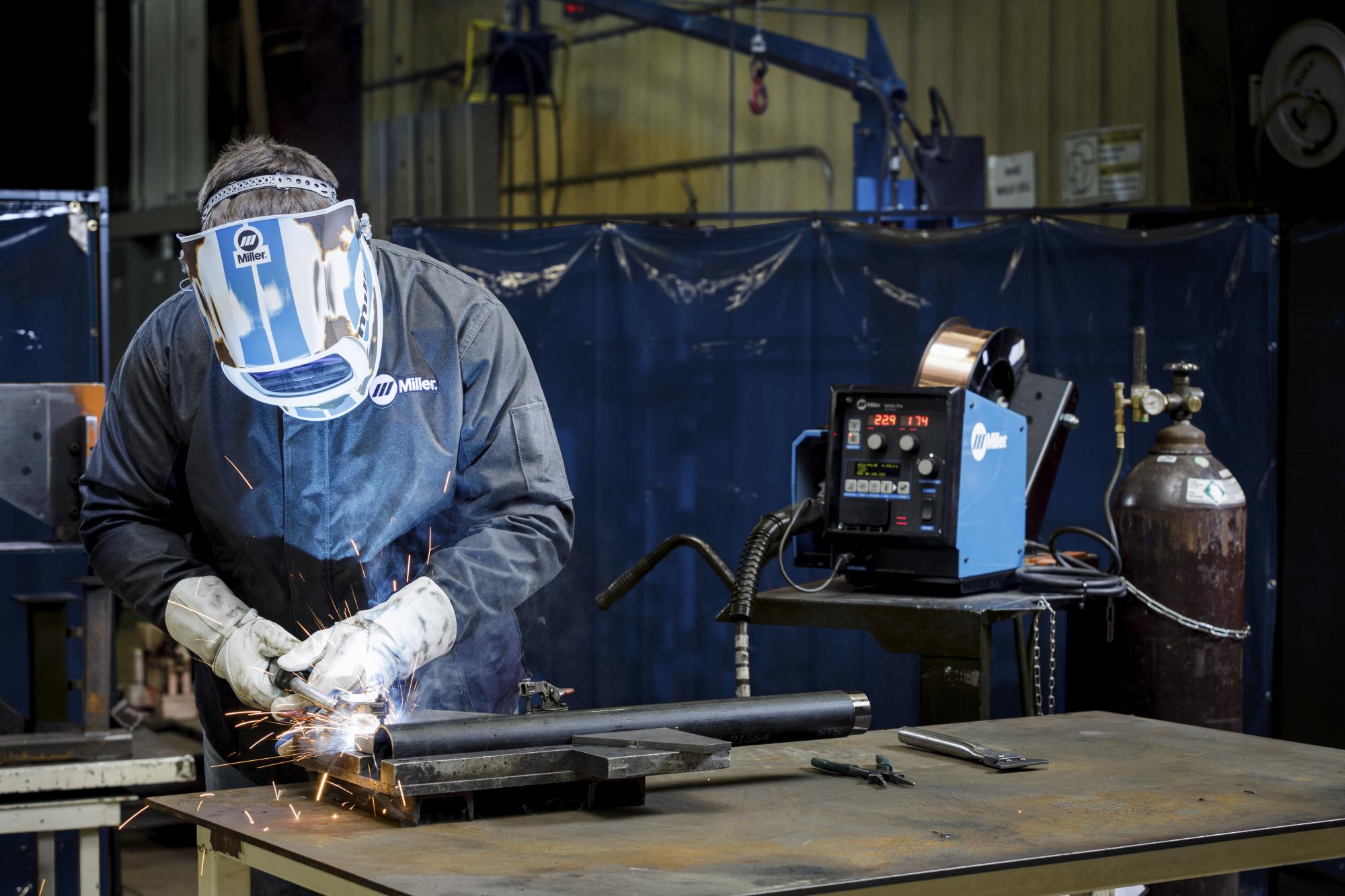
Looking to start your MIG welding journey? Here are some key tips to help you start out.
1) Keep a 1/4" to 3/8" stickout (electorde extending from the tip of the contanct tip)
Too Short Normal Too Long
2) For thin metals, use a smaller diameter wire. For thicker metals, use a larger wire and a larger machine. Most machines will come with recommendations for welding capacity and settings charts. This chart will help you select the best wire for you.
3) Make sure to use the correct wire type for the base metal being welded. Use stainless steel wires for stainless steel, aluminum wire for aluminum, and steel wires for steel.
4) The proper shielding gas is key in a good weld. When MIG welding steel you can use either CO2 or 75% Argon/25% CO2. 75/25 will give you the best overall results and less spatter compared to pure CO2 shielding gas. When welding aluminum pure argon is used. When welidng stainless steel a tri-mix (Helium/Argon/CO2) mix will give you the best results but also a 98% Argon/2% CO2 or 97% Argon/3% CO2 will work as well.
5) In order to keep control of your weld bead it is important to keep the wire directed at the leading edge of the weld pool.
6) When welding out of position (verticle, horizontal, or overhead welding), keep the weld pool small for best control, and use the smallest wire diamter size you can.
7) One of the most important things to remember is to make sure that your machine and welding gun is set up for the selected wire. Make sure your contact tip, gun liner, and drive rolls all match to the wire size you are using.
8) Change the gun liner every so often and cleand the drive rolls occasionally, keep the gun nozzle clean of spatter. Replace the contact tip if blocked or feeding poorly.
9) Keep the gun as straight as possible when welding to avoid poor wire feeding.
10) Use both hands to steady the gun when you weld. This will help you have smoother and more consistent welds.
11) Keep wire feeder hub tension and drive roll pressure just tight enought o feed wire, but do not over tighten. When the hub and or drive rolls are over tightened you will have wire feeding issues.
12) Keep wire in a clean, dry place when not welding, to avoid picking up contaminats that lead to poor welds.
13) Use DECP on the power source when welding with gas. (Plug the gun into the postive terminal and ground to negative terminal. Reverse Polarity). USE DECN on the power source when flux core welding. (Plug the gun into the negative terminal and ground to the positive terminal. Straight Polarity).
14) A drag or pull gun technique will give you a bit more penetration and a narrower bead. A push gun technique will give you a bit less penetration and a wider bead.
15) When welding a fillet, the leg of the weld should be equal to the thickness of the parts welded.
Good Weld Travel too fast Travel too slow Voltage too low Voltage too high Amperage too low
Amperage too high Less stickout, no gas