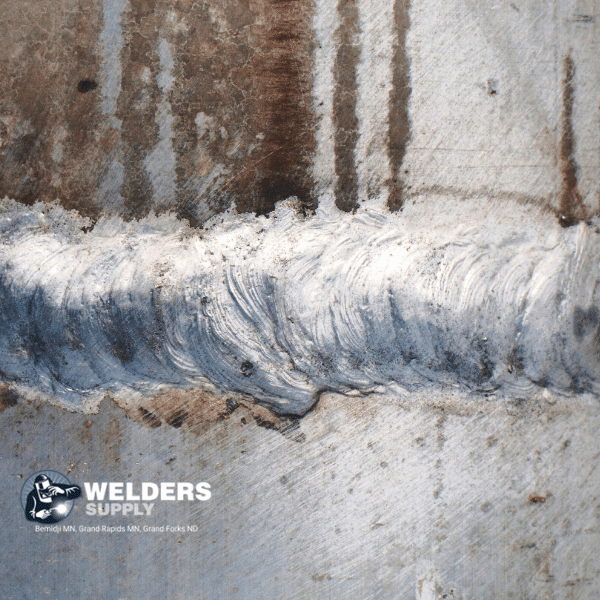
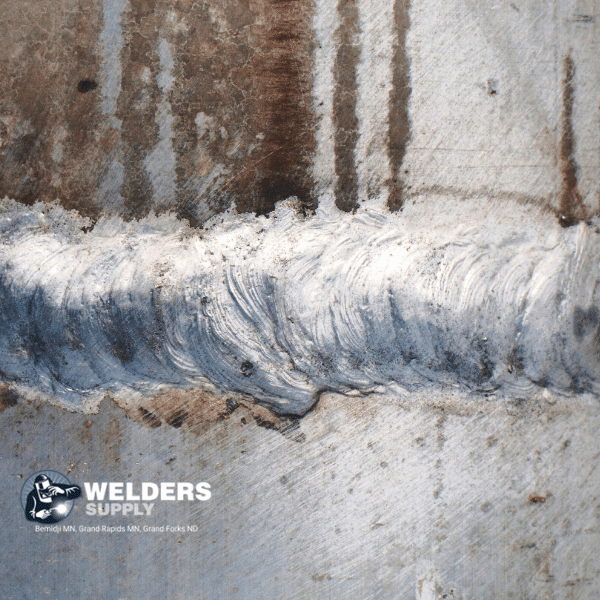
Tips for Welding Aluminum
Aluminum is a commonly welded metal because of its versatility and low-temperature requirements. Aluminum is challenging for beginners because it shrinks, warps, and easily breaks. However, like any new skill, welding this flimsy metal becomes easier with practice.
If you're starting your career as a welder, it's best to learn as much as possible before taking on aluminum. For example, the most common wire alloy is ER4043, followed by ER5356.
Books and manuals will be valuable resources, but you may need insider tips for welding aluminum. The following tips can help you get your footing.
Tips for Welding Aluminum
It may take some practice to master welding aluminum, but follow these tips to help you get started.
Keep the Material Clean
Cleanliness is an essential part of welding aluminum. Your material must be thoroughly cleaned before you can weld it. Use a hand or wire stainless steel brush to clean the aluminum.
If you use a power wire brush, keeping the machine at low pressure and RPMs will reduce the smudging of the surface. Whether you choose a hand brush or wire brush, ensure that it's clean and safe to use on aluminum.
Use the Appropriate Shielding Gas
Aluminum welding requires using 100% Argon shielding gas. This is essential for MIG Welding and TIG Welding. Ensure flow rates are maintained at 20-30 cubic feet per hour.
Use a Spool or Push Pull Gun
If you're MIG welding aluminum, you'll need to use a spool or push-pull gun. Using a spool gun enhances the feeding of soft aluminum wires, eliminating the potential for wire bird nesting.
A push-pull gun has a motor that pulls the wire through the liner, while another motor assists by feeding it through. This is an ideal solution for welding a significant amount of aluminum or when you need to weld away from the power source.
Tip Placement
Keep the welding tip an appropriate distance away from the work area. If it is near the material, it could cause the wire to burn back into the contact tip. This error will cause feeding problems.
Additional Tips for Welding
It's best to avoid large weave beads on aluminum. Instead, when significant filet welds are required, use multiple passes with straight beads to provide a better appearance, reducing the chance of burn-through, cold-lapping, and other welding defects.
When using a push travel angle, maintain 10-15 degrees. Ensure you are pushing the gun to avoid porous, dirty welds. Remember that you'll need to increase speed as the material becomes hotter.
Do you need welding supplies to help your career blossom? Contact Bemidji Welders Supply today.